Lectures, industry examples, step-by-step analysis of (dis-)advantages of various solution principles, but also identification of bearing requirements based on systems requirements and discussion of the do's and don'ts of specific principles. Multiple hands-on case studies from industry are included as guided team exercises.
Course material: printed reader containing a copy of the slides of all modules.
In precision motion systems, the focus is often on the actuated degrees of freedom (DoF) since these involve actuation, position sensing and motion control. In most/many cases, however, the non-actuated, constrained DoFs are equally important since these are exposed to similar disturbance forces as the actuated DoFs and accuracy requirements are comparably challenging.
Known solutions for constraining degrees of freedom in precision motion systems are roller bearings, flexure bearings, gas bearings and active/passive magnetic bearings, but what technology fits your application best? In order to answer that question one needs to understand the essence, pros/cons and limitations of each of these bearing technologies.
In CD players that were developed in the 1980s, originally, a swing arm supported by roller bearings was used to move the optical pick-up unit from the inner to the outer radius of the disk and to accurately follow a particular track. In later generations, driven by a smaller pitch and tighter accuracy requirements, the swing arm was replaced by a translational guide way based on sliding contacts for coarse positioning, combined with a flexure bearings for fine positioning of the pick-up unit in radial and focus direction.
Typically, when designing precision motion systems, various design parameters have to be balanced and simultaneously optimized, such as range of motion, accuracy and reproducibility, stiffness and damping. Although sliding and also rolling contacts suffer from stick-slip behaviour and (virtual) play, cost and complexity are low and performance might be good enough for coarse positioning. When low friction and hysteresis is required, or strict requirements on particle generation hold, it may be advantageous to fully separate surfaces via full film bearings, either aerostatic or hydrostatic. For large range of motion in vacuum conditions, such as in electron microscopes, E-beam inspection or EUV lithography systems, active magnetic bearing systems (AMBs) are highly advantageous. Despite higher cost, these systems have the additional advantage that frame vibrations can be isolated from the motion stage. When only small translations or rotations are required, flexure bearings can provide excellent reproducibility, particularly if manufactured monolithically. These bearings, however, suffer from parasitic stiffness and have very little damping.
This course will focus on the design, modelling and implementation of bearing elements in precision motion systems. We will discuss the trade-offs between performance on the one hand, and cost and complexity on the other hand. Both passive and active bearing technologies will be extensively discussed. We will focus on different application areas, such as medical equipment, machine tools, scientific instrumentation and semiconductor applications.
Objective
Participants will acquire a mix of theoretical background, do's and don'ts and practical insight. After the course, participants understand the potential of the different bearing elements and systems and will be able to initiate, specify and guide the design and development, or select the proper off-the-shelf solution.
Target audience
The course is intended for engineers (both designers and architects) who want to gain more insight in the options and limitations for applying various bearing types in precision motion systems and how to get to a favorable design.
It is recommended that participants already have a Bachelor or Master degree in mechanical- or electrical engineering, mechatronics, physics, or an equivalent practical experience, and have some basic understanding of Precision Engineering. This course is particularly suitable for engineers having followed the course in 'Mechatronics’ (part 1 and/or 2).
The course attracts participants from both the Netherlands and abroad, creating an international atmosphere that fosters valuable knowledge exchange. If you're traveling from outside the country, you can find useful travel information here.
Program
Introduction bearing technologies
- Definitions
- Balancing stiffness, motion range, accuracy, reproducibility, and cost complexity
Sliding contacts
- Virtual play, stick-slip, positioning against stops, ball-cone sliding contact, self-breaking, inertial sliding, kinematic mount w/flexible contacts
- Case: Wafer load (high frequency dithering) / Scan-up-scan-down
Roller bearings
- Load capacity, Hertzian stiffness, lifetime, preloading, alignment, hysteresis
- Bearing / spindle run-out / error motion
Performance vs. Costs
- Case
Full film (aerostatic) bearings
- Working principle, stiffness compensation, bearing, static and dynamic stiffness, tilt stiffness
- Air bearing support, preloading
Case: Wafer stage H-drive
Flexure bearings
- Elastic elements, reinforced flexures, stiffness reduction, large stroke flexures, negative stiffness, folded leaf spring, monolithic / clamped flexures, microslip, reproducibility, flexure damping
- Flexure guide ways, rotation tables
Case: EUV Wafer handler gripper
Active magnetic bearing systems
- Magnetic bearing systems compared to conventional bearing systems
- Virtual stiffness, actuator residual stiffness (position dependency), isolated metrology loop, force centre, over-actuation.
- Case: Nano Imprint stage
- Case: Maglev stage
Special topic
Wrap-up
Methods
Certification
This course is certified by the European society for precision engineering & nanotechnology (euspen) and the Dutch Society for Precision Engineering (DSPE), and leads to the ECP2-certificate.
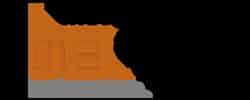